Image
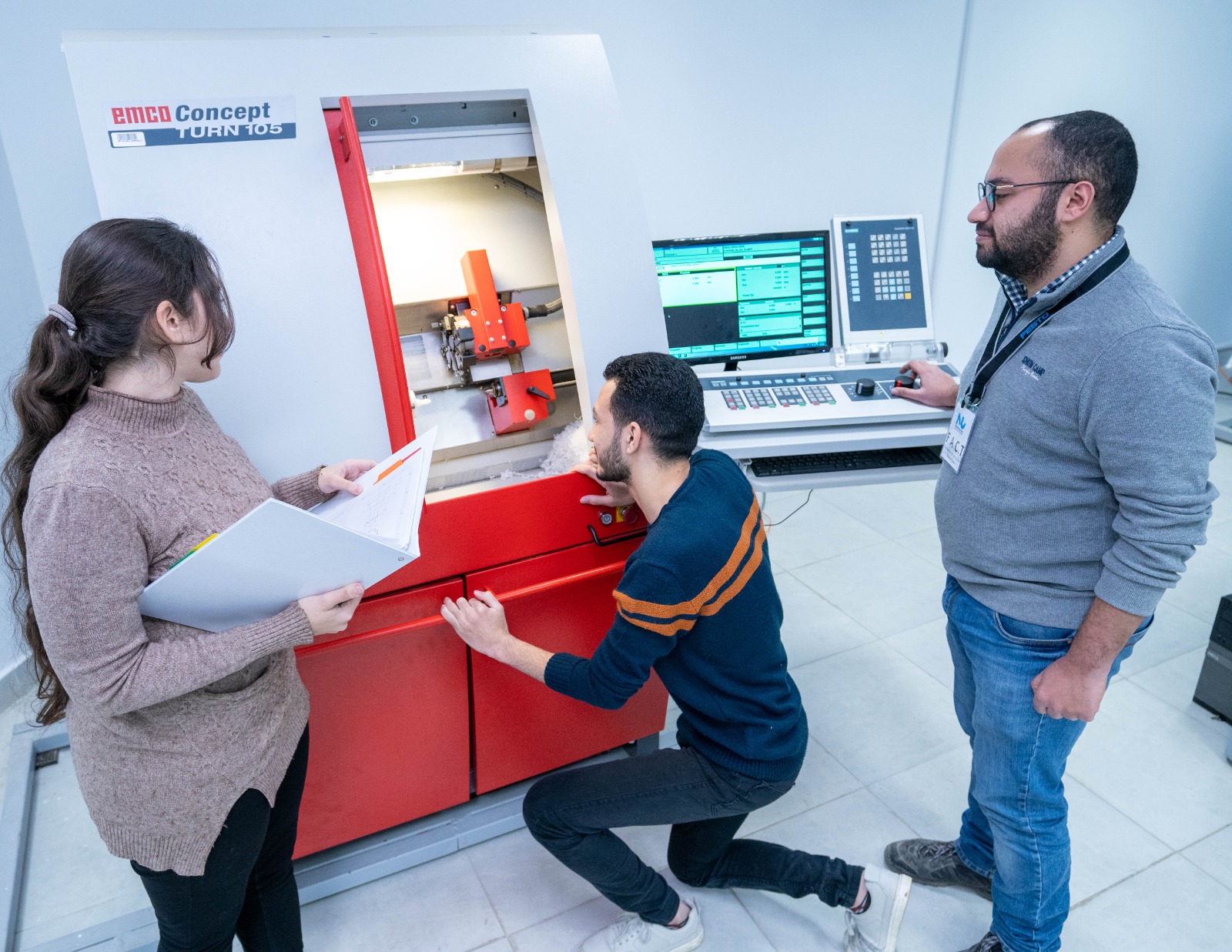
CNC Advanced - FANUC Series 21 Lathe and Mill (CNC 421)
Course Details
|
4 days/32 hours |
---|---|
|
Basic CNC technology |
|
CNC |
|
English |
CNC machines are one of the most important equipment used in industry to produce parts. This workshop will provide the necessary know-how based on hands-on training on real industrial equipment upon the ISO G-Code language, FANUC variant.
- Brief introduction about the ISO G-Code language for advanced programs: tool compensations, coordinate system management, main and sub program, cycles.
- Principles of ISO G-Code FANUC 21 structured program.
- Set of instructions for tool length and radius compensation for lathe and milling machines.
- How to start and how to close the tool compensation inside a NC program.
- The User Coordinates System: how to set and how to change it inside a program.
- How to write a main program and how to write a sub program.
- The combination of main and sub programs for repeating a job for an exact number of items; how to call a sub program.
- The combination of main, sub programs and User Coordinate Systems.
- The set of cycles included for Milling operations.
- The set of cycles included for Turning operations.
- Samples according to FANUC Series 21.
- understands the basics on how to write a structured program for a CNC Machine equipped with FANUC Series 21 Numerical Control
- understands how to control the System of Coordinates inside a NC program
- understands how to control the tools dimensions inside a NC program
- is able to start and stop in the right way the tools dimensions compensation within turning or milling NC programs
- knows the structure and the syntax to create a main or a sub program according to ISO G-Code FANUC Series 21
- knows how to call a sub program inside a main program or another sub program
- knows how many sub program levels can be used
- knows the set of standard cycles for Milling operations
- knows the set of standard cycles for Turning operations
- is able to simulate the tool path and understand it